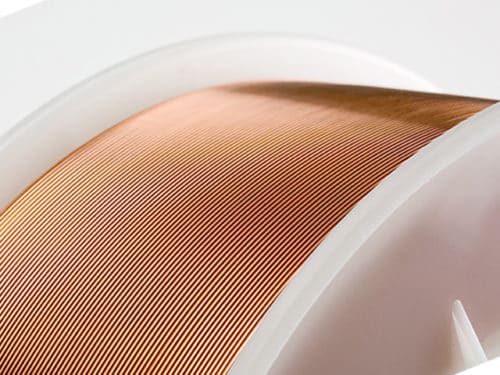
Flux cored wires
Nippon Steel Welding & Engineering (NSWE) seamless flux and metal cored wires.
NST has been a main supplier for Nippon Steel flux cored wires (FCW/FCAW) welding wires for 30 years. Over the years, as NST established a closer relationship with NSWE, our highly qualified NST staff has also taken part in the further development of NSWE flux and metal cored wire formulas for the most demanding, high requirement offshore welding operations.
Production method
From the first time they were developed NSWE seamless flux and metal cored (FCW) wires have continually been adapted to new conditions and requirements from our customers. The unique properties of NSWE’s innovative seamless FCW wires have been developed in step with the renewal of production techniques. The excellent properties are mainly achieved using NSWE’s ICF production process (In-line continuous filling), by welding the outer metal layers, joining the seams together and perfectly sealing the flux inside at the time of production.
Hydrogen content
The biggest advantage with NSWE seamless FCW wires is its extremely low hydrogen content, achieved with heat treatment as an important part of the production process. This technique prevents post production atmospheric moisture absorption as well. In comparison, conventional folded type flux cored wires has an open seam which allows moisture to penetrate the flux, resulting in an almost hourly increase in hydrogen pickup when exposed to moisture.
Copper coating
The seamless design also enables the wire to be copper coated, which is not possible with conventional folded wire types, as the copper would leak into the flux. The copper coating and exact symmetrical cross-sectional shape results in excellent wire feeding properties, tip abrasion resistance and stable targeting, making it ideal also for mechanized/robotic welding purposes.
Benefits of NSWE flux cored wires:
- Very low hydrogen content in the weld metal
- Superior targeting and wire feeding properties
- Very good and consistent mechanical properties
- Less downtime and increased productivity
- Excellent conductivity and stable, spatter-free arc
- Reduced contact tip consumption
- Longer shelf life with less storage preconditions